High Temperature Hydrogen Attack (HTHA) is a damage mechanism with a significant impact in the power plants, fertilizers and refinery industry. It results in gradual and relatively slow degradation of the vessel material during particular time period, but more rapid degradation thereafter.
This process can be monitored by inspection surveys to identify degraded areas, and engineering assessments to assess fitness for continued service.
Hydrogen Induced Damage Mechanism
Hydrogen is one of the fundamental elements in many industrial processes, but its presence can also be a potential source of damage.
When hydrogen combines with high temperatures and pressures, the material characteristics of carbon steel or low alloy steel can be negatively altered.
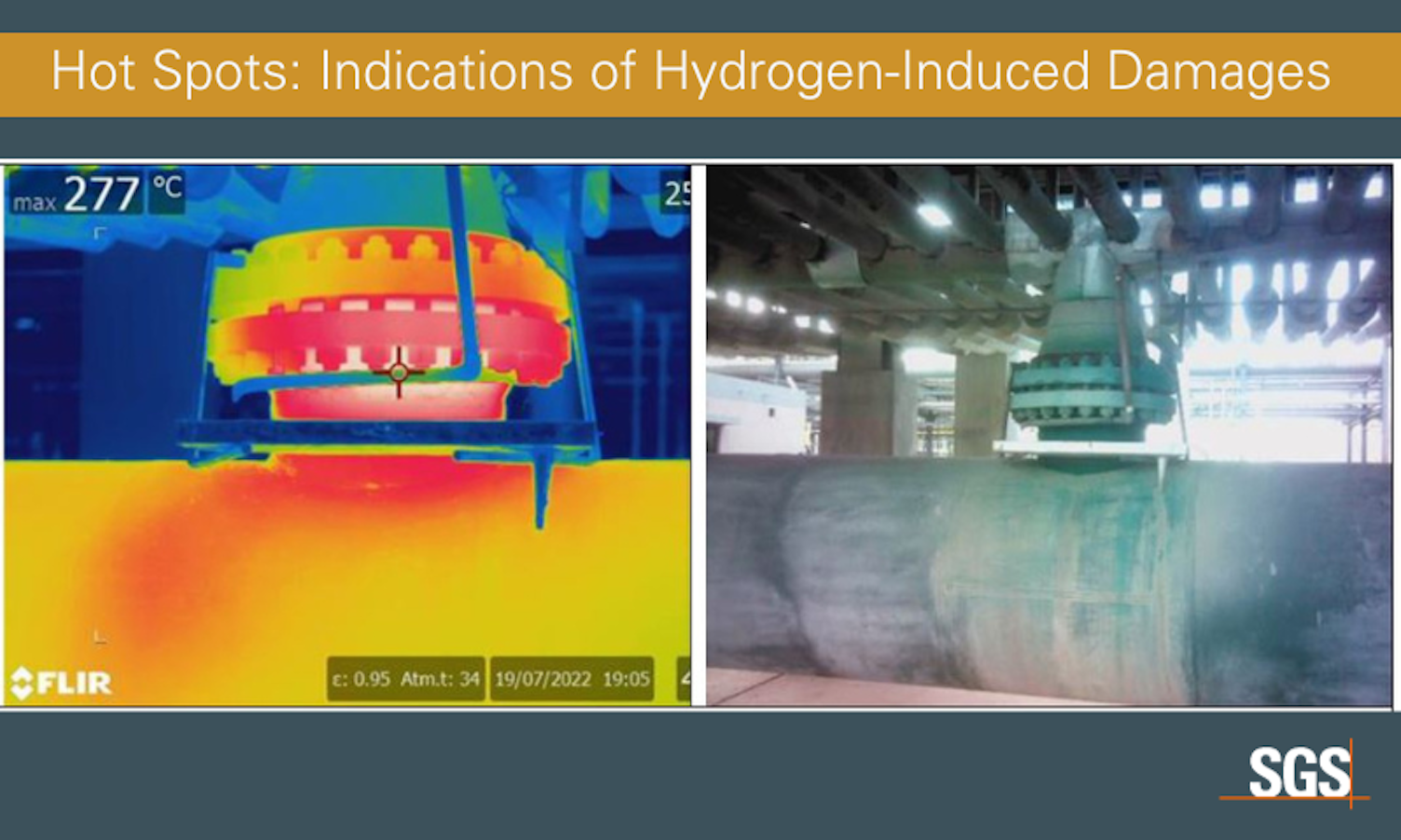
There could be various types of hydrogen induced damages, which include:
- Hydrogen Embrittlement
- Hydrogen Assisted Cracking
- Hydrogen Induced Cracking (HIC)
- High Temperature Hydrogen Attack (HTHA)
The HTHA damage process progresses through three distinct stages:
- The evolving period, when changes cannot be detected. During this period, methane pressure builds up without causing significant damage and very small voids forms which are microscopic in size.
- Rapid fissure formation and growth, with rapid deterioration. During this phase, the micro-voids join up to form fissures and macro cracks.
- When carbon is exhausted and materials properties stabilize on the final, deteriorated level.
Engineering FFS Assessment and Remaining Life
Fitness for continued service must be assessed by using a practice such as API RP 579, when HTHA flaws are discovered through inspection.
The method of assessment will depend on the nature of the discovered flaws.
- In case of micro-fissuring, the depth of the affected layer has to be established through NDT. The structural integrity of the unit, based on the properties of the unaffected remainder of the wall, will be assessed using the methodology of Section 4 (General Wall Loss).
- If cracks are evident, the cracks have to be sized and assessed using Section 9 of the Recommended Practice.
- The significant fraction of the service life required for development when remaining life is considered, at the stage of assessment, undetected attack may be present in the “unaffected area”. Frequent monitoring, surface cladding and rerating are measures that can be considered in such cases.
SGS's Approach to Address Challenges
SGS takes a multi-faceted approach to HTHA detection and mitigation. With a focus on safeguarding industrial assets from the effects of hydrogen damage, our inspection services aim to ensure the safety, reliability, and longevity of critical infrastructure in high-risk environments.
To address the challenges posed by HTHA, SGS offers a comprehensive approach to inspection services. This approach includes techniques like:
- TULA (Base material)
- Time of Flight Diffraction (ToFD) for examining longitudinal and circumferential welds
- Phased Array Ultrasonic Testing (PAUT) for nozzle and pipe-to-fitting welds
- Total Focusing Method (TFM) or Full Matrix Capture (FMC) (Base materials)
- Velocity ratio measurements (Base material)
- Spectrum analysis (Base material)
Inspection Planning and the Use of Advanced NDT
An initial assessment of the vessel will identify susceptible regions of equipment hot spots.
Generally, on a process vessel the inspection would consist of inspecting a band 50mm wide on either side of all longitudinal, circumferential or nozzle to shell welds, as well as an area of 300mm X 300mm at the area of highest hydrogen partial pressure.
Further to the above, all longitudinal and circumferential welds are also inspected using the Time of Flight Diffraction ultrasonic technique with steep angle transducers.
TOFD (Weld Scan)
The welds selected for inspection shall be scanned for HTHA-scatter and cracks or crack-like indications in the heat effected zone, by scanning a-centrical to both sides of the butt welds using high frequency probes.
During this inspection only the lower (inner) third of the weld HAZ shall be investigated. The sensitivity shall be such that all relevant indications are detected on a suitable ToFD calibration/reference piece.
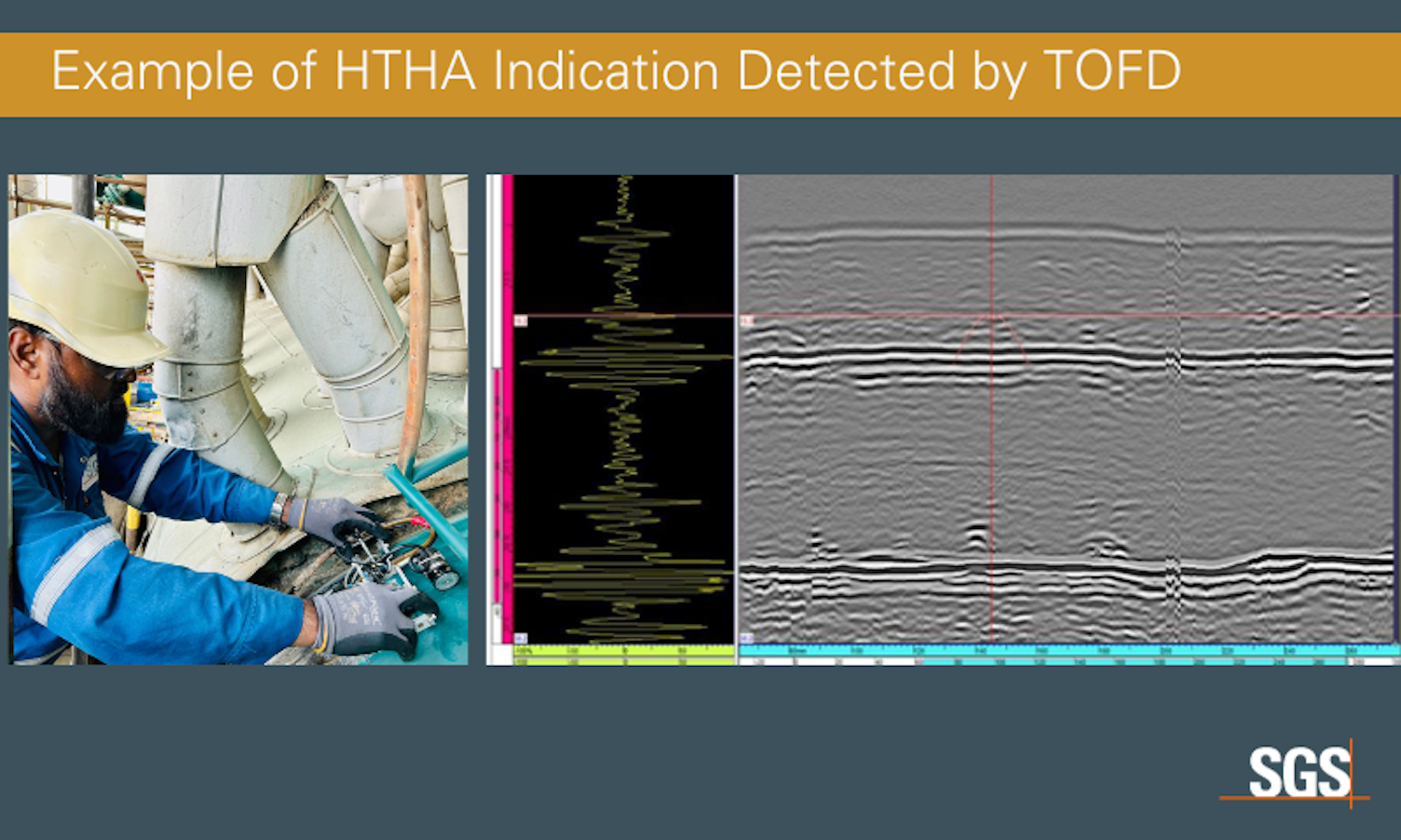
PAUT (Weld Scan)
Using Focused PA, the welds selected for inspection shall be scanned for HTHA-scatter and cracks or crack-like indications in the heat affected zone.
During this inspection only the lower (inner) third of the weld and at least 10 mm parent material shall be investigated using a sensitivity of 1.5mm SDH with angles (preferably) under 50°. The sensitivity shall be demonstrated by detecting all relevant indications on a suitable PA or ToFD calibration/reference piece.
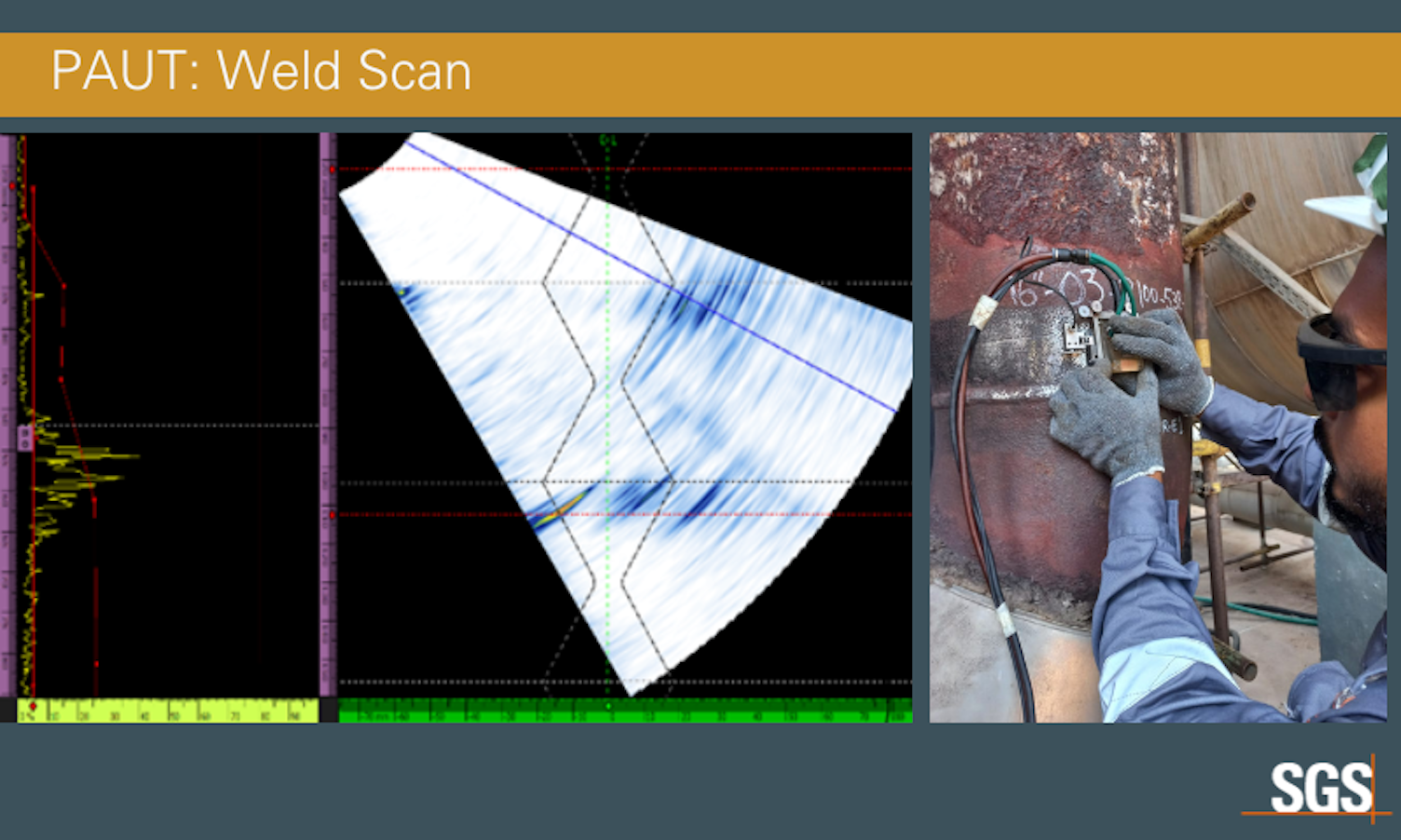
TULA – ToFD Ultra Low Angle
ToFD Ultra Low angle probe of 10 MHz twin crystal using Different roof angles is very useful in detecting HTHA and can be used for Up to 100mm of wall thickness. TULA is specifically used for the screening of base material.
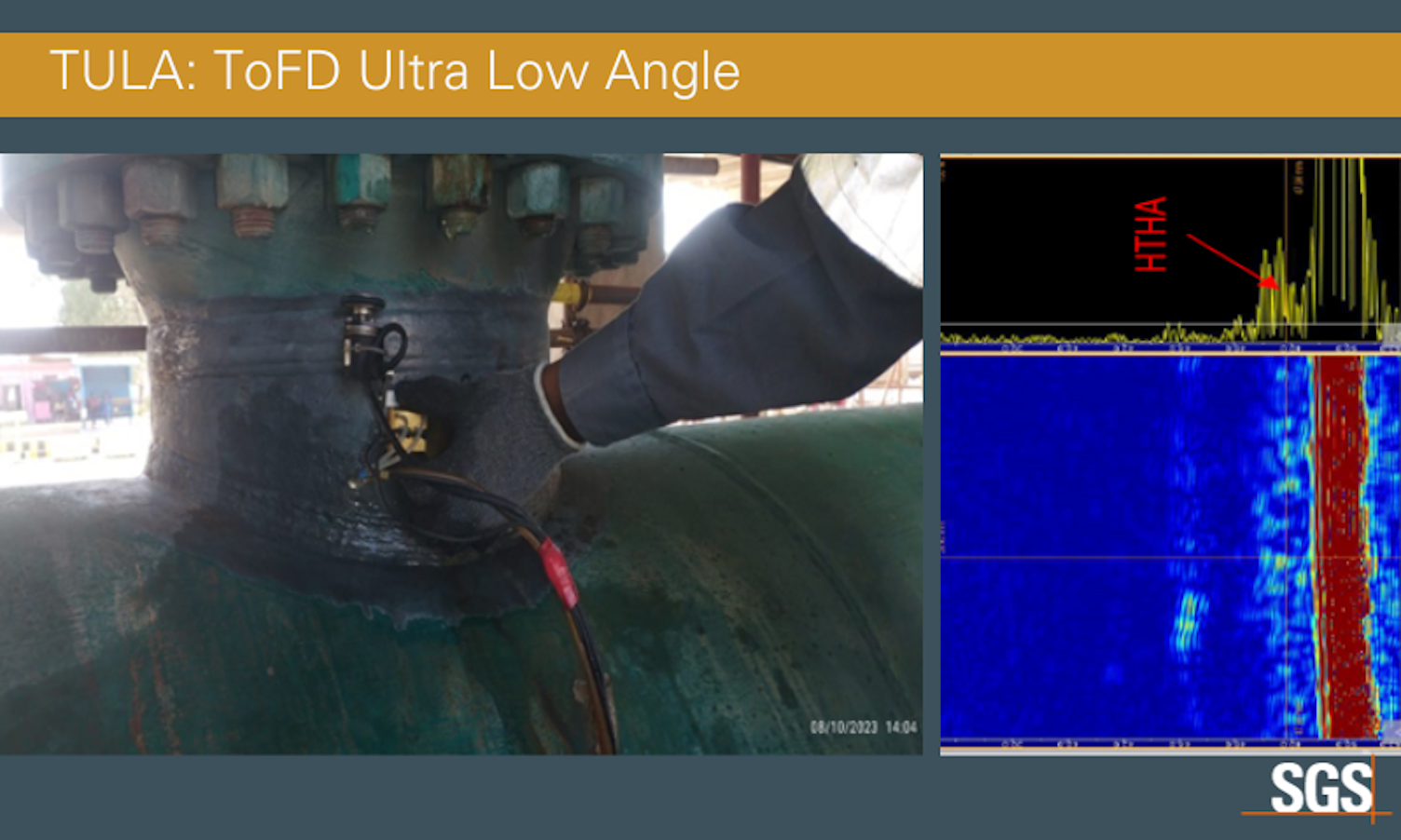
PAUT Backscattering
PAUT Backscattering is done over a 50 mm wide band on either side of all longitudinal, circumferential and full penetration nozzle welds as well as a 1m2 area of the shell material at the location of the highest operating temperature and hydrogen partial pressure.
Where HTHA is detected in either the parent material or welds this has to be confirmed by s supplementary techniques in order to further differentiate between HTHA and inclusions or other impurities. This is a two-step approach and consists of Velocity Ratios and Fast Fourier Transformation techniques. Where no evidence of HTHA is detected by the primary inspection technique the inspection is considered complete.
FMC/TFM (PAUT)
- Minimum 32 array probes
- High Frequencies
- High density reconstruction grid
- Can be combined with PAUT
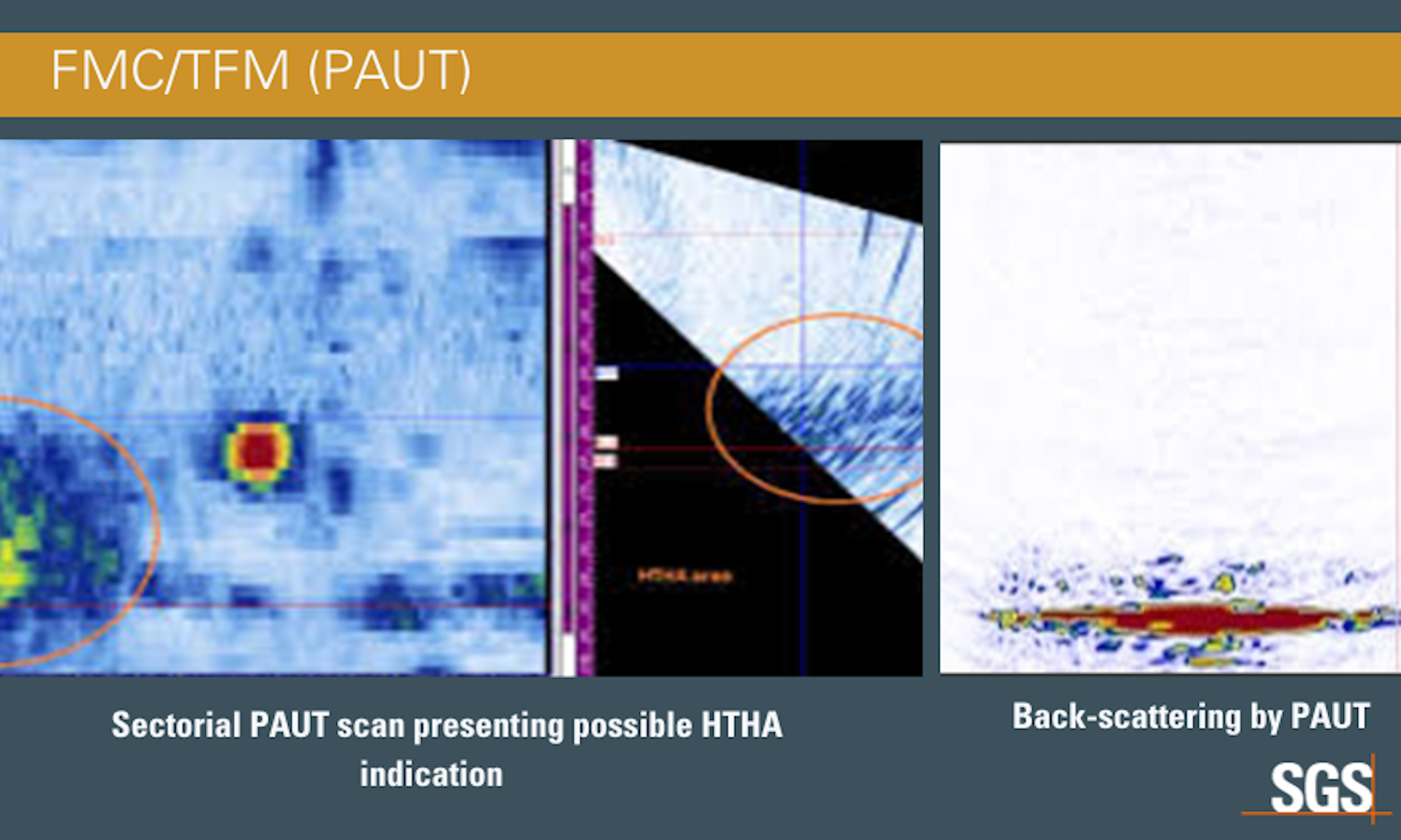
Velocity Ratio Measurements
This technique relies on measurement of transit times and can be accomplished with a conventional digital UT flaw detector.
A 5 MHz 0º broadband compression wave and 0º broadband 1/2” 5 MHz incident shear wave is used for measurement of transit times. Special viscous couplant is used for the 0º incident shear wave to transmit the ultrasonic energy.
Using the same spot location first the longitudinal velocity and then the shear velocity is measured on the basis that the thickness does not change in that location. The ratio of Vs/VL should be <0.55. Ratios above this value are an indication of HTHA and if this is found the Fast Fourier Transformation technique is used.
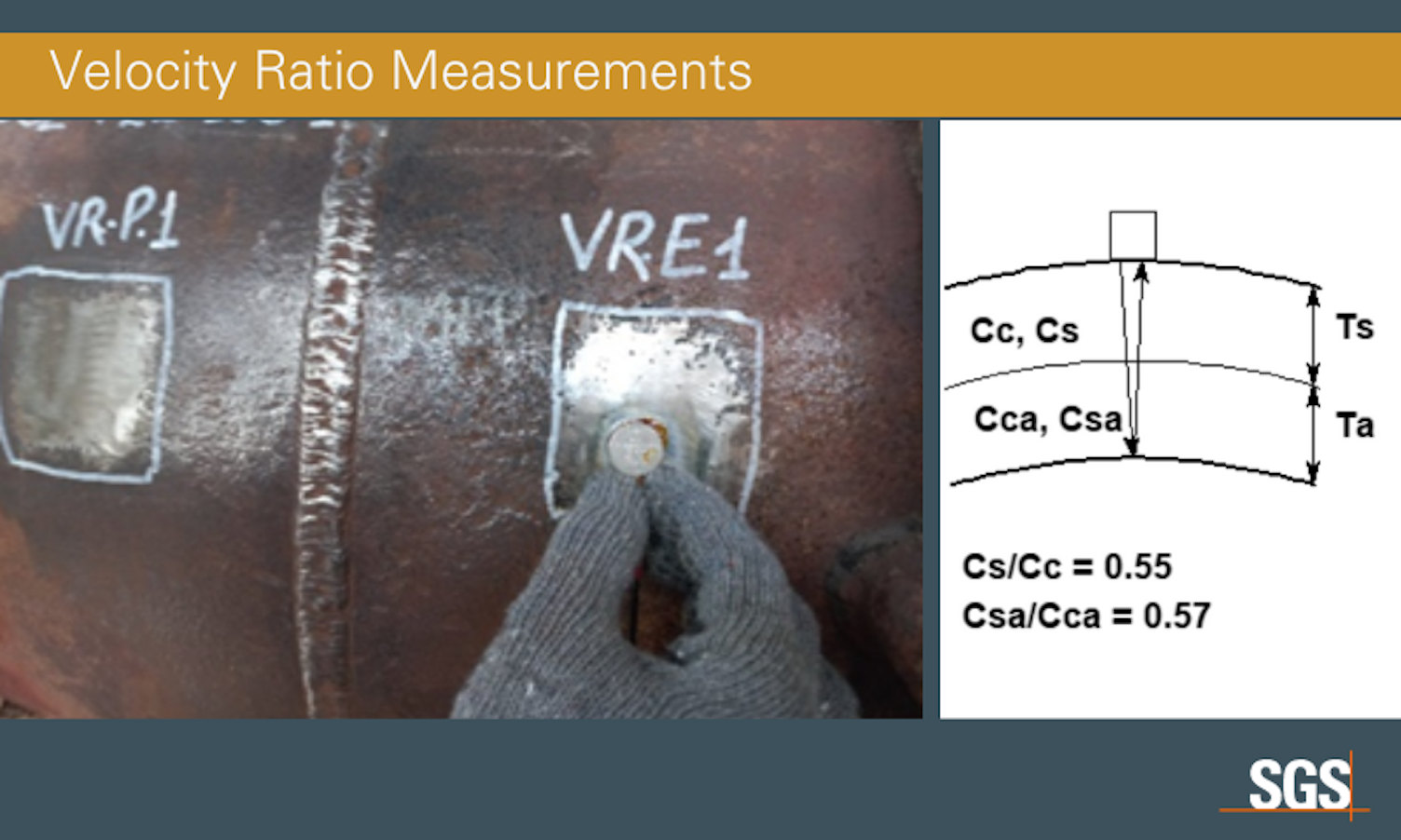
- Sound velocity will 10% reduce if HTHA attack is present
- Absolute sound velocity can not be measured, because exact value of mechanical wall thickness is not available
- By taking the wall thickness measurement with shear and compressional waves, information about attack can be obtained
- Use only for verification (supplementary technique)
Spectrum Analysis
Parent Material:
- Based on frequency dependent attenuation
- Use only for verification (supplementary technique)
- Reference on clean sample is required
Welds:
- Based on reflection with high frequencies from tips
- Use only as supplementary technique for verification (no weld defect)
- Reference on clean sample is required
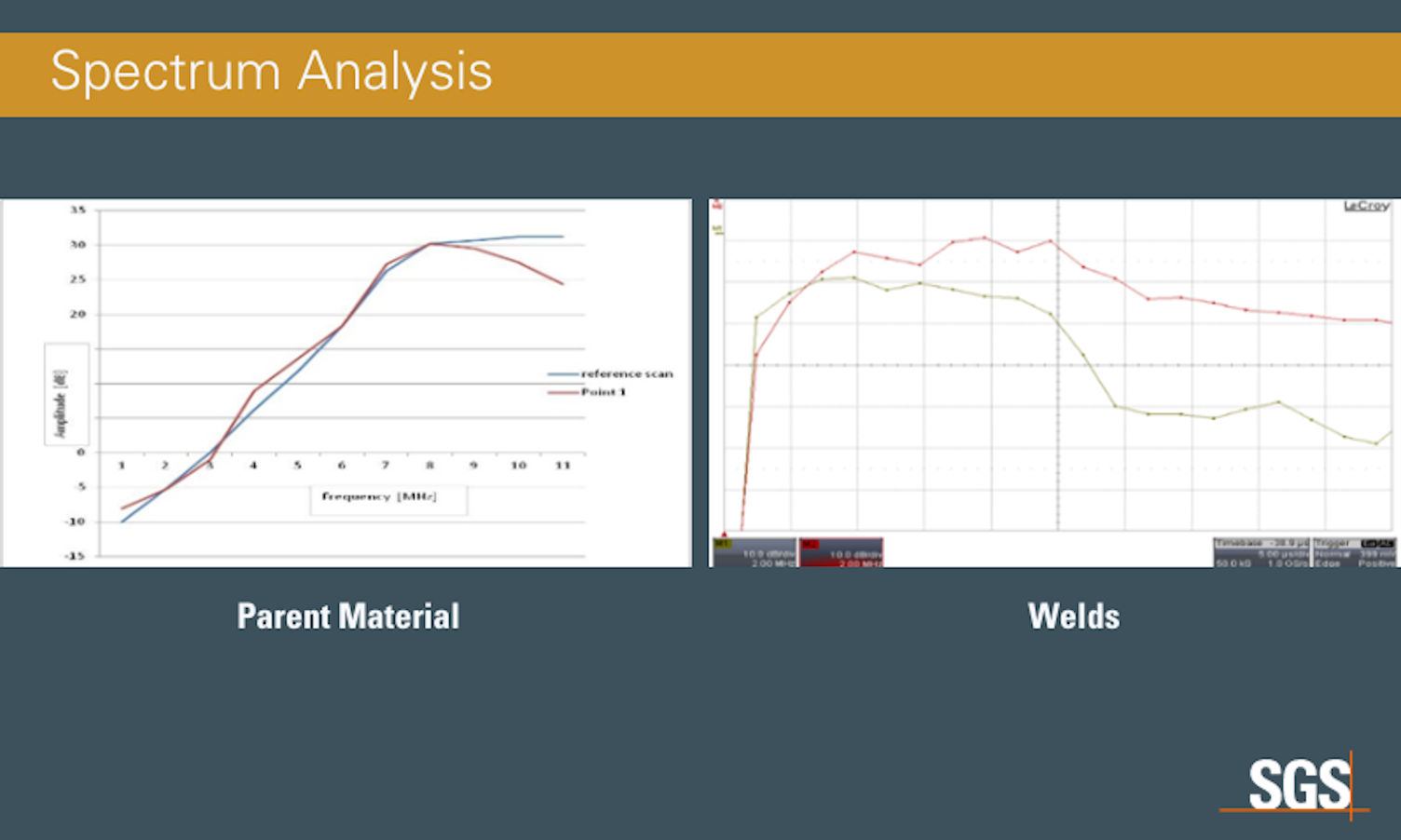
Material replication and sample analysis can be used to aid in the understanding of the stage of damage. Samples analyzed at >800x magnification can detect the voids which signify the early stages of attack. However, Metallurgical replica’s, can normally only detect the advanced stages such as fissuring.
- Stage 1 Hydrogen (H+) reacts in the material with the carbon to resulting in voids filled with CH4 (Methane)
- Stage 2 Micro cracks (fissures) will appear on the grain boundaries, filled with Methane (size typically around 0.05mm)
- Stage 3 Aligned fissures will connect
- Stage 4 Macro crack
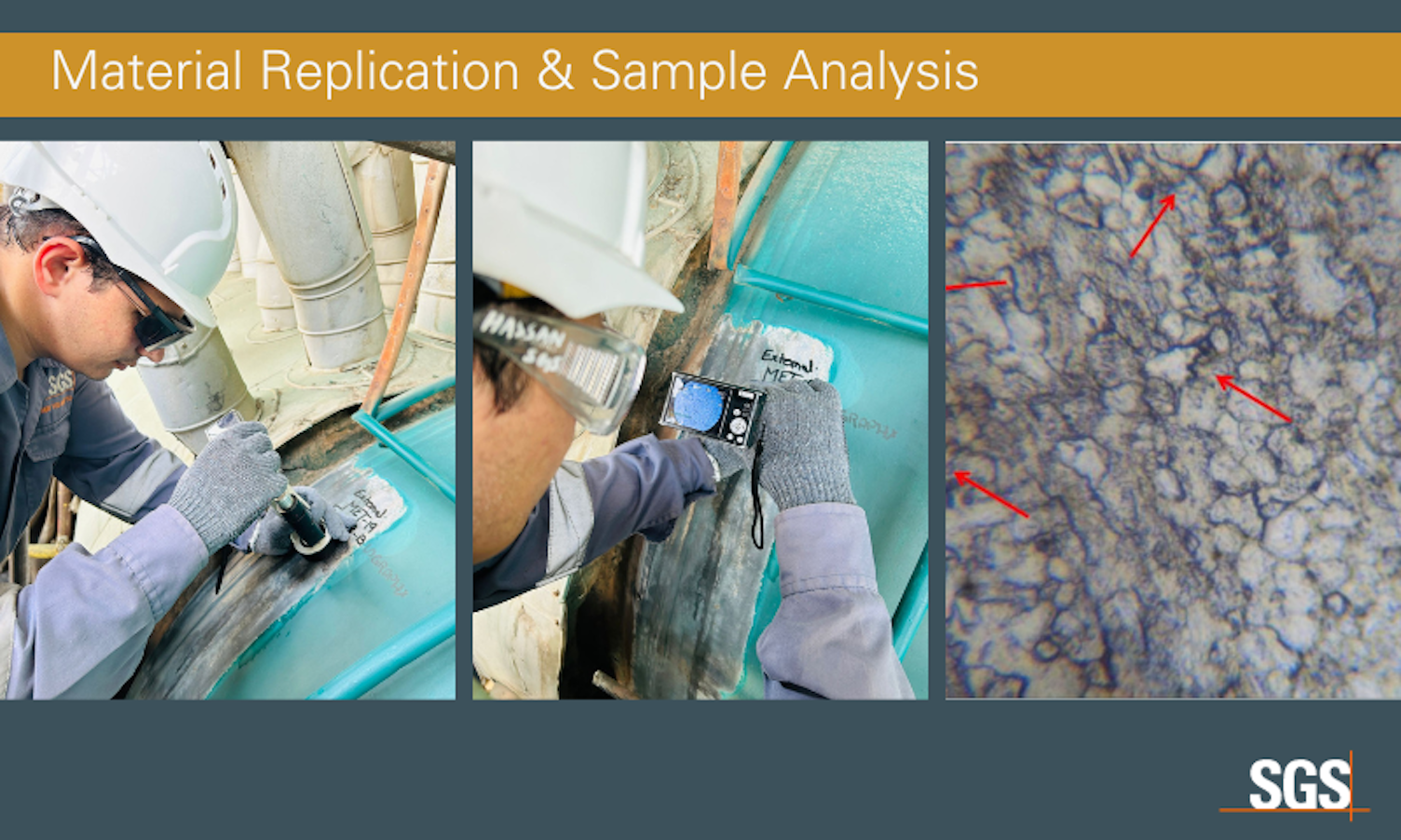
Hardness Testing
HTHA can cause a decrease in the hardness of the affected material, surface decarburization results in a decrease in hardness and increase in ductility of the material near the surface. So hardness testing can be used to detect HTHA damage.
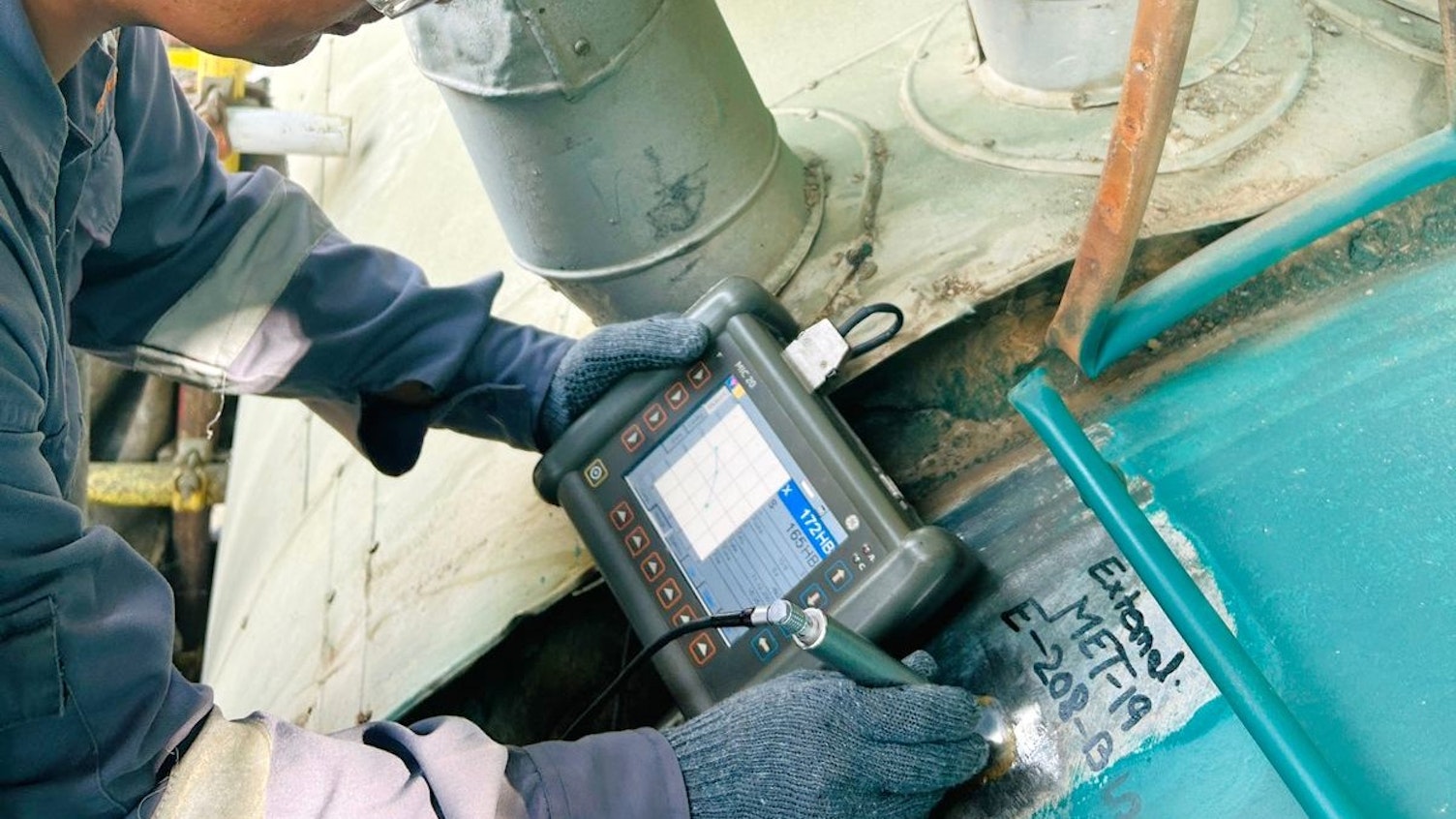
Conclusions
HTHA is a damage mechanism, it demonstrates a slow development in the beginning, later mixed with the fast acceleration once HTHA have started, if not detected in early stage it may increase risk of macro or large cracks.
To deal with such damage complications, proper monitoring inspection and NDT strategies must be in practice such as thermal Inspection to be carried out periodically to monitor hot spots and to identify places of excessive risk.
Then combination of risk based techniques and advanced NDT will make sure the early detection and effective mitigation of damage.
About SGS
We are SGS – the world’s leading testing, inspection and certification company. We are recognized as the global benchmark for sustainability, quality and integrity. Our 98,000 employees operate a network of 2,650 offices and laboratories, working together to enable a better, safer and more interconnected world.
SGS Building, Street no. N 203,
Jebel Ali Free Zone North,
Dubai, United Arab Emirates