Advancements in robotic technology are revolutionizing the inspection of storage tanks and pressure vessels, significantly reducing the risks associated with human entry. A recent inspection project for buried tanks in Pakistan serves as a shining example of how innovative approaches can enhance safety and efficiency in mechanical integrity assessments.
Case Study Highlights: Buried Tank Inspection in Pakistan
The project involved the internal inspection of two buried tanks under strict constraints, allowing only minimal human entry to set up equipment. The goal was to assess mechanical integrity and suitability for continued operation, ensuring compliance with industry codes and standards.
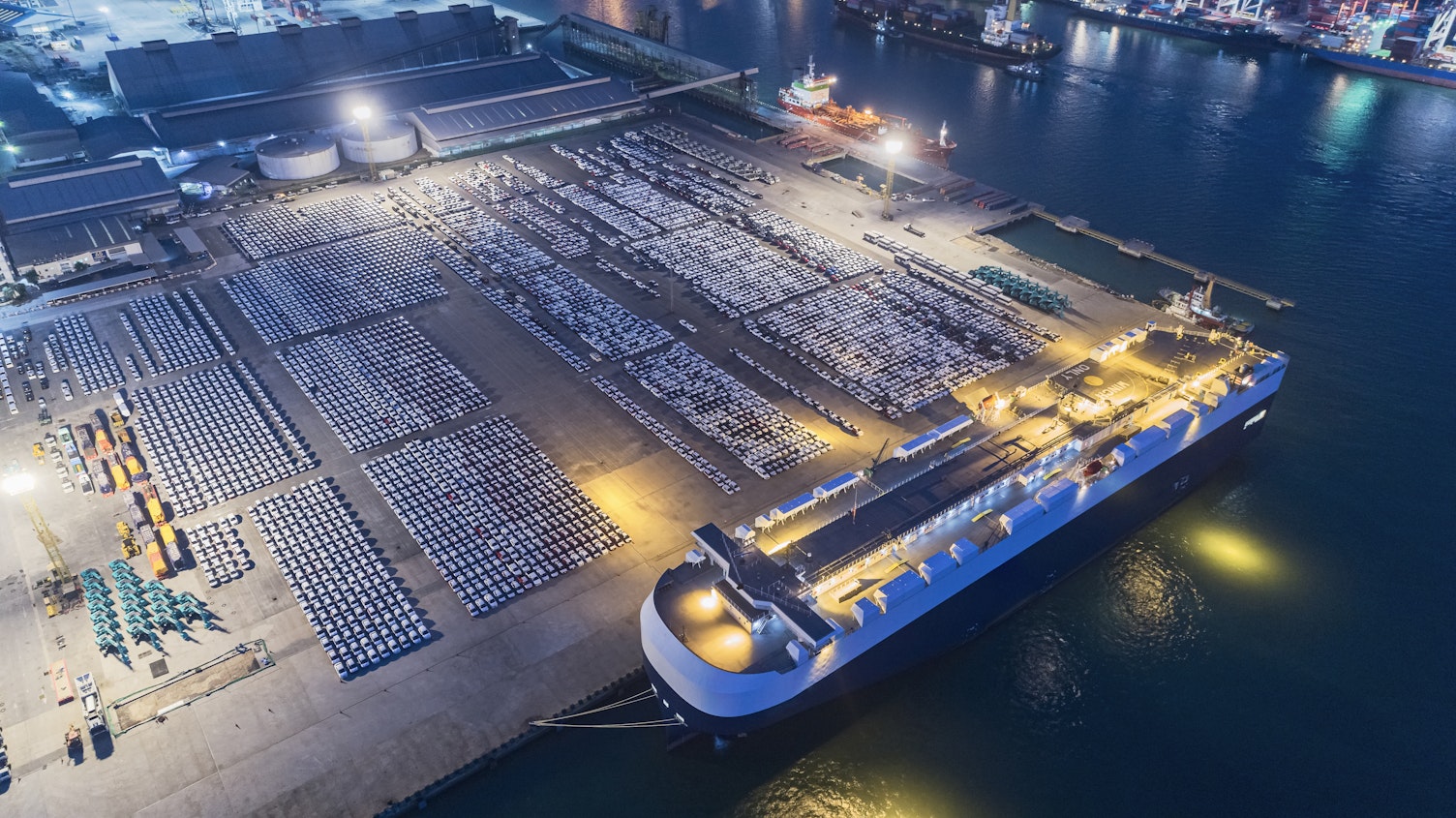
Challenges Overcome
Unlike above-ground tanks, buried tanks present unique difficulties:
- Restricted Visual Access: Operators had no direct visual contact with the inspection equipment
- Minimal Entry Protocols: Human entry was restricted to the initial setup phase
- Complexity in Equipment Movement: Remote control of robotic systems required precise coordination
Despite these challenges, the inspection team, equipped with advanced robotic crawlers and high-resolution cameras, ensured a comprehensive assessment.
Advanced Tools and Techniques
The inspection was conducted using cutting-edge technology to minimize human risk:
- Robotic Crawlers for Visual, UT gauging & Holiday Testing: Enabled close visual inspection, ultrasonic thickness gauging, and holiday testing, all controlled remotely
- RMS 2 Corrosion Mapping Equipment: Delivered high-speed, accurate evaluations of the tank’s internal surfaces, identifying potential areas of degradation
- Short Range Ultrasonic Testing (SRUT): Focused on nozzle inspections and hard-to-access areas
High-resolution cameras provided real-time 360° visuals to track robotic crawler positions, ensuring full control and coverage of the tank's internal environment.
Key Achievements
- First-of-its-kind Implementation: This marked the first use of RMS 2 for buried tank inspection in Pakistan
- Remote Monitoring: All activities were controlled and monitored externally, adhering to strict safety protocols
- Comprehensive Integrity Assessment: The integration of multiple inspection methods ensured a detailed evaluation of the tanks’ condition
Conclusion and Future Implications
This project underscores the potential of advanced robotic technologies to transform traditional inspection methods. By eliminating the need for prolonged human entry, these solutions not only enhance safety but also improve accuracy and efficiency. The success of this inspection sets a benchmark for similar projects globally and highlights the critical role of innovation in addressing industry challenges.
As the push for safer and more effective inspection practices continues, embracing these advanced methodologies will be key to maintaining the integrity of vital assets in oil, gas, and other sectors.
About SGS
SGS is the world’s leading Testing, Inspection and Certification company. We operate a network of over 2,700 laboratories and business facilities across 119 countries, supported by a team of 99,250 dedicated professionals. With over 145 years of service excellence, we combine the precision and accuracy that define Swiss companies to help organizations achieve the highest standards of quality, safety and compliance.
Our brand promise – when you need to be sure – underscores our commitment to trust, integrity and sustainability, enabling businesses to thrive with confidence. We proudly deliver our expert services through the SGS name and trusted specialized brands, including Brightsight, Bluesign, Maine Pointe and Nutrasource.
SGS is publicly traded on the SIX Swiss Exchange under the ticker symbol SGSN (ISIN CH0002497458, Reuters SGSN.S, Bloomberg SGSN:SW).
C/O Horizon Djibouti Terminals Limited (HDTL),
Doraleh Container Terminal, Djibouti