In the highly competitive and evolving landscape of global manufacturing, operations, and manufacturing executives are continuously seeking ways to enhance efficiency, reduce waste, and maximize profitability.
The adoption of Lean Manufacturing principles has emerged as a cornerstone for achieving Operations Excellence, particularly within the Middle East dynamic manufacturing sector.
With SGS’s active presence and local expertise in Middle Eastern countries like the UAE, Saudi Arabia, Turkey, and Pakistan, we are uniquely positioned to drive significant advancements in this sector.
This article delves into how Lean principles are applied to manufacturing and operations to foster a culture of continuous improvement, focusing on the unique approach and benefits offered by the SGS Productivity solution.
Understanding Lean Manufacturing and Operations Excellence
Lean Manufacturing is a systematic approach aimed at minimizing waste within manufacturing systems while simultaneously maximizing productivity. It involves a set of practices that focus on value creation for the end customer with minimal waste.
Operations Excellence, on the other hand, is a broader term that encompasses not only efficient production processes but also the optimization of all organizational operations to achieve superior performance and competitiveness.
Lean Manufacturing Operations
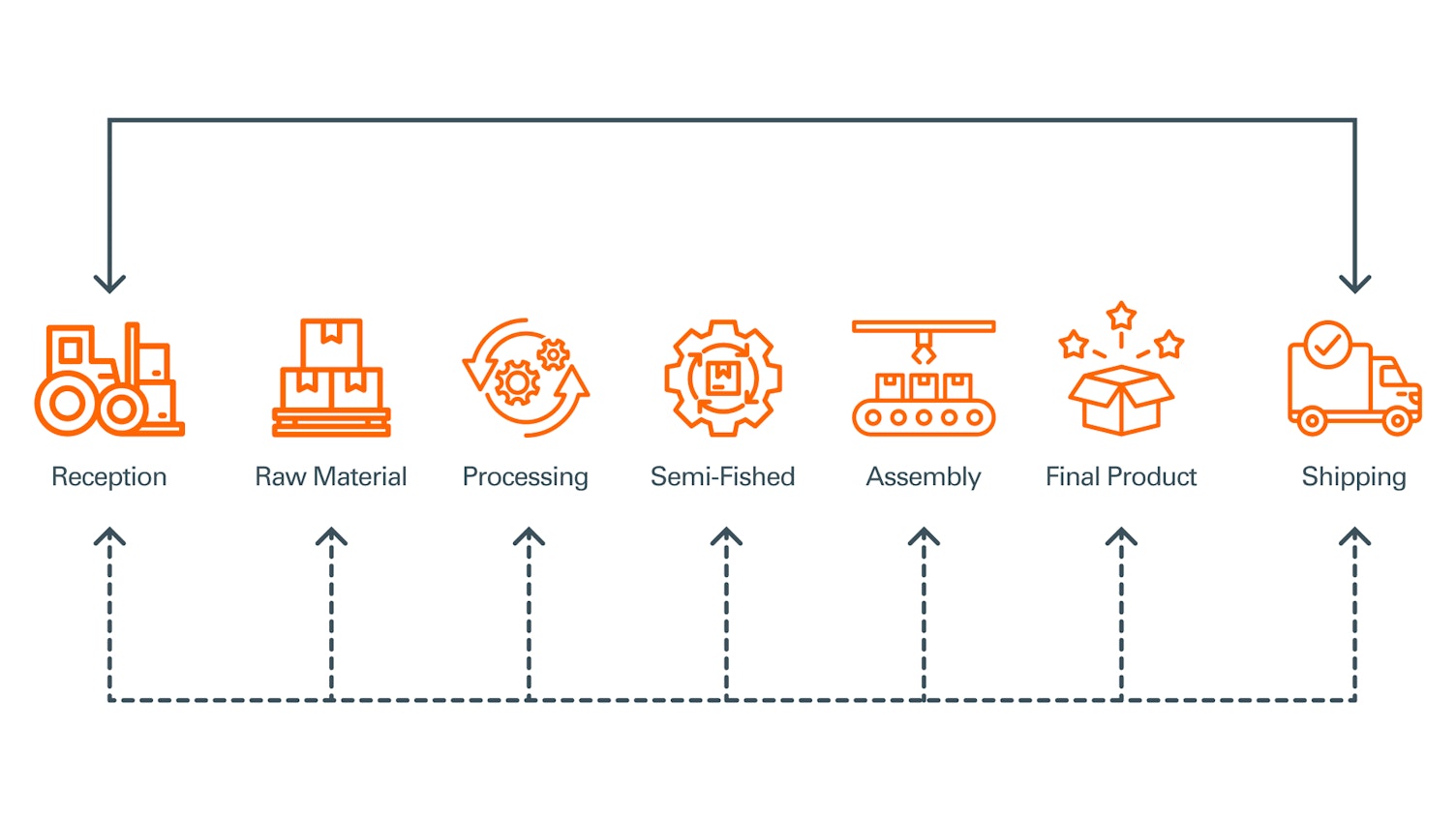
- Core Focus on Production Processes and Internal Logistics
The focus is primarily on production processes and internal logistics, crucial for adding value to products, supported by meticulous planning, maintenance, plant quality, and engineering activities.
- Comprehensive Coverage from Dock to Dock
From the moment materials are received until the finished products are shipped, our Lean Manufacturing - Operations methodology covers all stages of transforming raw materials into finished goods. This includes all processes of handling and processing, ensuring seamless and efficient operations throughout the production chain.
- Flexibility in Processes
While most processes under this methodology are self-contained and highly repetitive, our methodology also provides the flexibility to manage transversal processes such as Lean Office. Additionally, it handles various industrialization projects and structural developments through Lean Project initiatives, enhancing versatility and adaptability in operations.
- Enhancing Operational Efficiency
By adopting this comprehensive approach, manufacturing companies in the Middle East can significantly enhance their operational efficiency, reduce waste, and increase productivity. This not only supports sustainable growth but also strengthens their competitiveness in the global market.
The SGS Productivity Solution: A Commitment to Results
At the heart of SGS Productivity solutions' success in implementing Lean Manufacturing and achieving Operational Excellence is a steadfast commitment to results.
This commitment is manifested through the delivery of annual savings that exceed the cost of services, surpassing customer expectations through cost-free diagnostics, tailored training, and hands-on engagement with operation teams.
Cost-Free Diagnostics: The Foundation of Improvement
The journey towards Operations Excellence with the SGS Productivity solution begins with a thorough diagnostic phase.
Before embarking on any project, SGS experts visit your plant to analyze the existing operations, identify potential for improvement, and ensure the profitability of the project.
This preliminary phase is crucial for defining a tailored improvement plan that anticipates the savings and outlines the necessary steps to achieve them.
Tailored Training: Empowering Teams for Continuous Improvement
Understanding that each client's needs are unique, the SGS Productivity solution offers customized training programs.
These programs are designed to equip operational teams with the knowledge and tools needed to implement Lean principles effectively.
Training covers a wide range of topics, including methodological guides, standards, and best practices, ensuring that teams are well-prepared to drive continuous improvement within their operations.
Operational Teams Tools for Excellence
To operationalize Lean Manufacturing and achieve Operations Excellence, the SGS Productivity solution focuses on key operational tools:
- 5S
This foundational tool helps organize the workplace in an efficient and effective manner, promoting safety and productivity. It lays the groundwork for employees to engage in continuous improvement practices.
- Polyvalence
Training teams to be versatile in their skills and capabilities ensures that operations can be agile and responsive to changing demands.
- Visual Board
Implementing visual management tools, such as parts boards, aids in the efficient organization of materials and information, streamlining processes and reducing waste.
- Improvement Ideas
An idea of improvement is an action that is proposed within the operational teams and that can improve its way of working.
- Communication System
Communication is the cornerstone of business management, encompassing both formal and informal systems. Informal communication aids in preparing formal communication, which is structured and regulated by a meeting map.
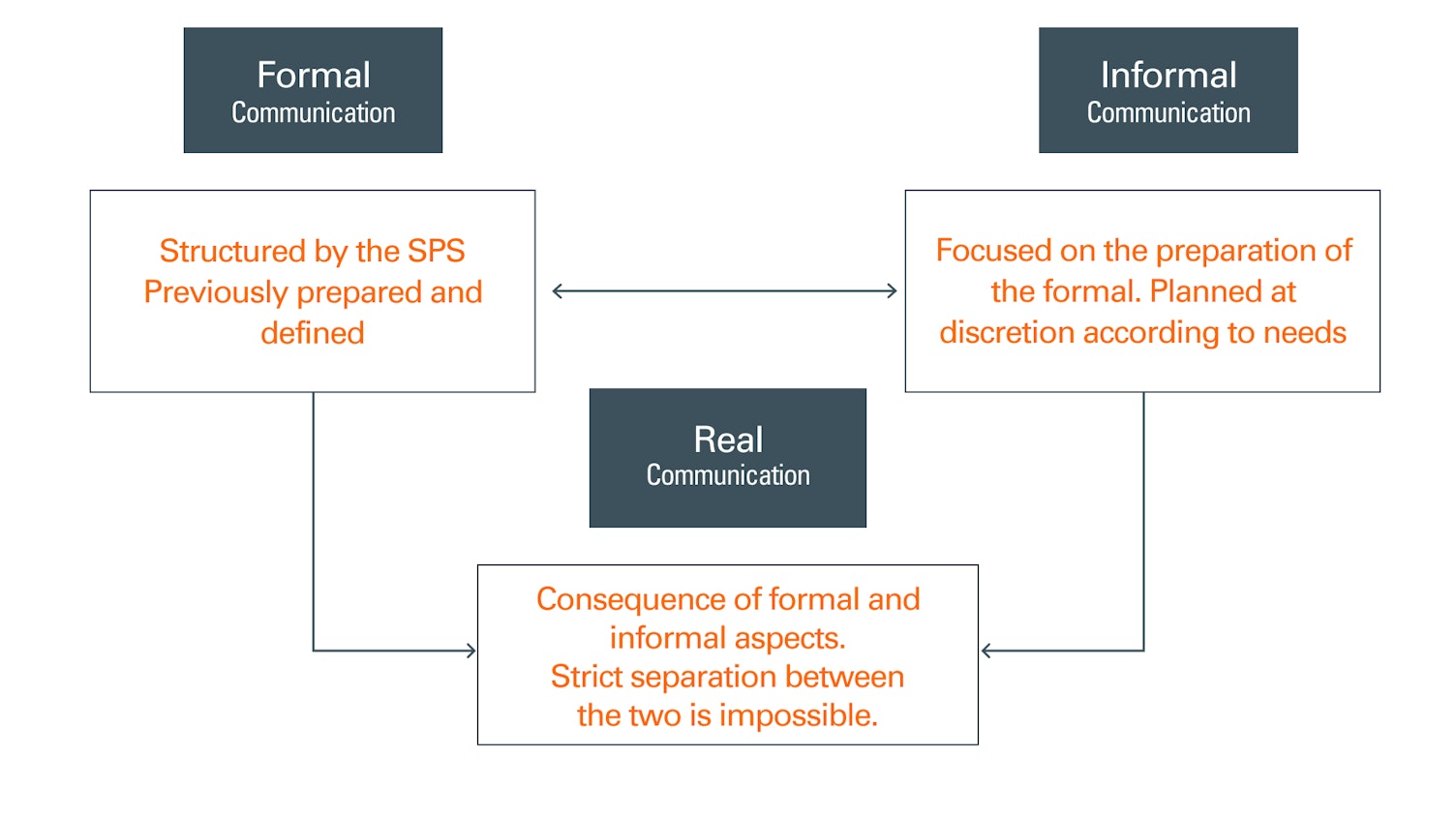
Structure of formal communication
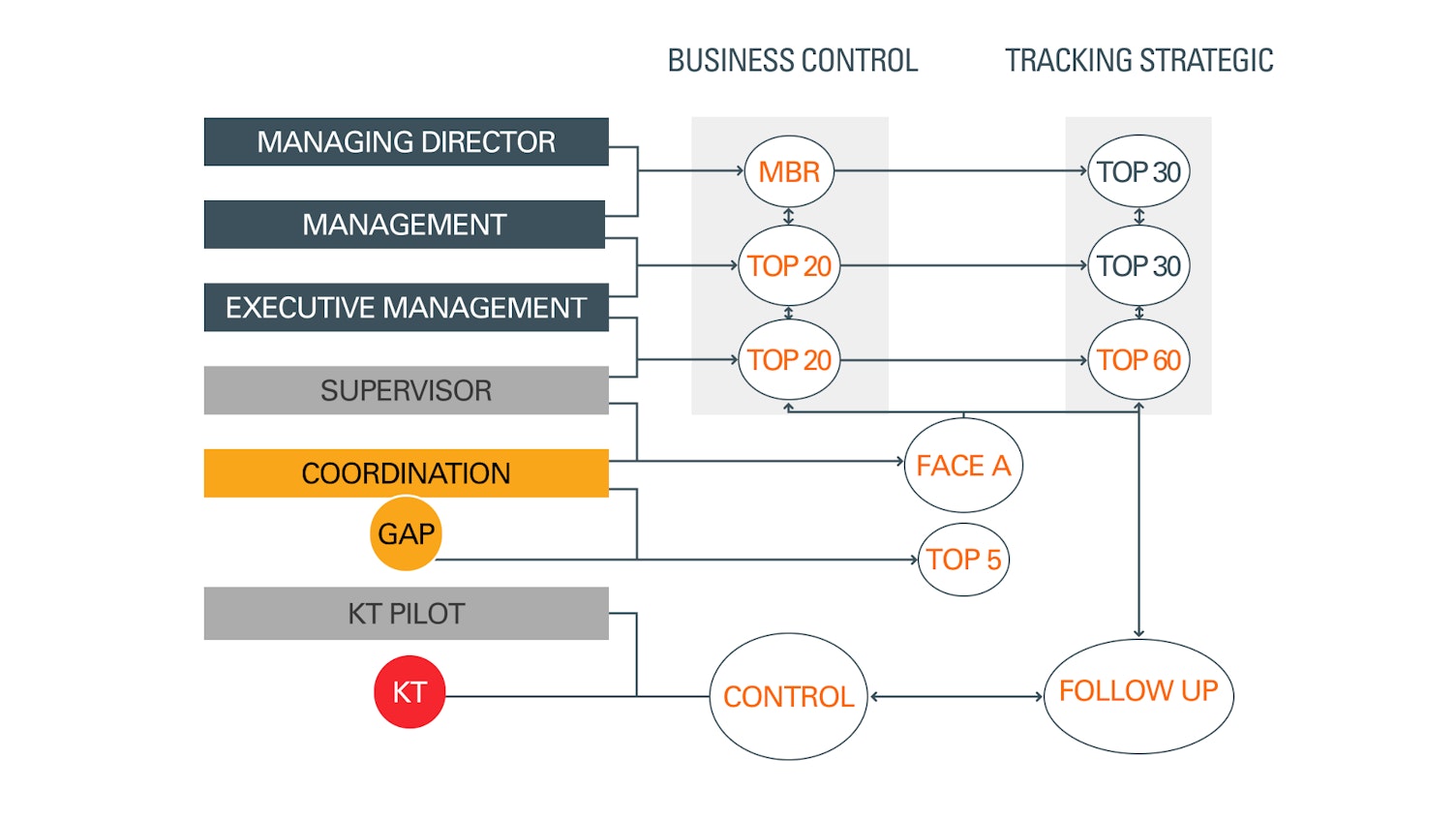
The Implementation Process: From Diagnosis to Extension
The SGS Productivity approach to implementing Lean Manufacturing and achieving Operations Excellence is structured yet flexible, designed to demonstrate tangible results as swiftly as possible
- Diagnosis and Improvement Plan
Initially, a comprehensive review of the company's areas is conducted, comparing each with the fundamentals of the system governing them. This leads to the development of a tailored improvement plan. - Pilot
Efforts are concentrated in a small area to prove the system's effectiveness early on. This pilot phase is crucial for refining the model before wider implementation. - Extension
Once the system is successfully developed in the pilot area, it is extended across the entire organization. This phase involves standardizing best practices and key aspects of improvement, ensuring that the benefits are realized across the board.
Realizing the Benefits
Adopting the SGS Productivity approach to Lean Manufacturing and Operations Excellence delivers significant benefits:
- Reduced Costs and Increased Savings
Streamlining operations and reducing waste directly contribute to lower operating costs and enhanced savings. - Improved Product Quality
Lean practices lead to processes that are more controlled and consistent, resulting in higher quality products. - Greater Employee Engagement
Employees become more engaged and invested in the success of their operations as they are empowered to contribute to continuous improvement efforts. - Decreased Stocks and Internal Logistics Throughout the Chain
Efficient processes reduce the need for excessive inventory and streamline internal logistics, further reducing costs and improving responsiveness.
Conclusion: Pioneering Lean Manufacturing Excellence in the Middle East
For Middle East manufacturing companies, the journey toward Lean Manufacturing and Operations Excellence is a strategic imperative to maintain competitiveness in the global market.
The SGS Productivity solution stands out by delivering a results-oriented approach that combines cost-free diagnostics, tailored training, and hands-on implementation of operational tools like 5s, improvement ideas, parts board and polyvalence.
By working side by side with operational teams, the SGS Productivity not only achieves but exceeds expectations, delivering tangible benefits that resonate throughout the organization.
Reach out to know more about SGS Productivity Solutions
About SGS
We are SGS – the world’s leading testing, inspection and certification company. We are recognized as the global benchmark for sustainability, quality and integrity. Our 99,600 employees operate a network of 2,600 offices and laboratories around the world.
Sin El Fil – Horch Tabet,
St. Georges Bldg, 9th Floor, 165165,
Beirut, Lebanon