When you outsource to suppliers, it is essential to ensure that the products supplied meet quality standards and that your suppliers adhere to laws and regulations. QA/QC inspections of supplier goods and services can help you to prevent potential issues early on and so avoid delays, extra costs, including fines due to lack of compliance, and loss of consumer confidence in your brand.
Our inspections and supplier evaluations help you control quality, ensure regulatory compliance and protect your reputation.
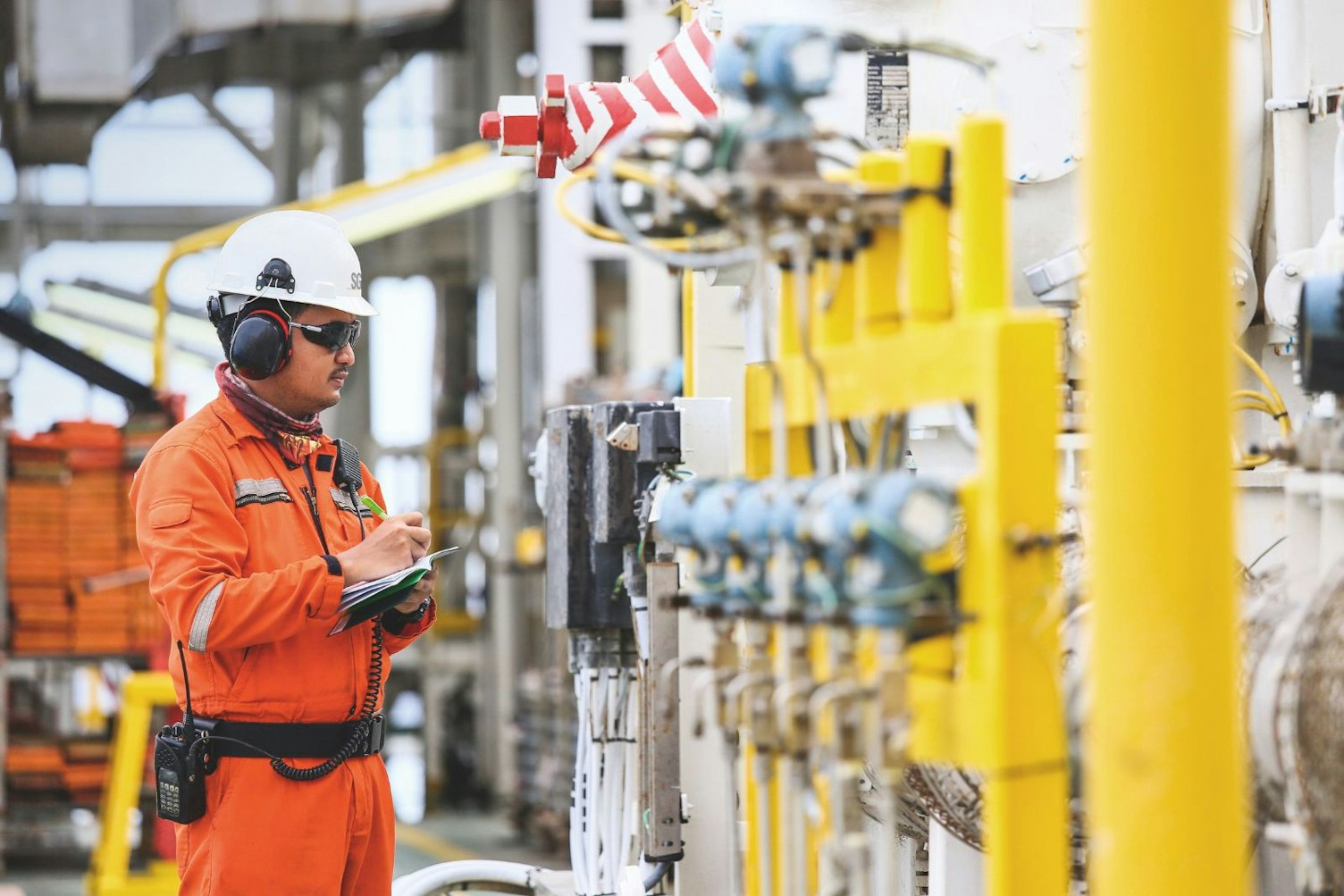
Second and third party inspections
Control the quality of the materials, components and equipment that you purchase. We will enable you to identify defects and potential quality risks at the source and ensure conformity with applicable international or local codes, standards and technical applications. Through our global network, we provide local inspectors, reducing travel times and ensuring that your inspections are performed by experts with essential local knowledge. Our global quality management system enables streamlined delivery.
Our second and third party supply chain inspection services include:
- Source inspection
- Manufacturing process inspection
- Coating inspection and failure analysis
- Dimensional inspection
- Documentation review
- Quality inspection of final products
- Packing and loading isnpection
- Storing and handling inspection
- Visual inspection
- Welding inspection
- Witness tests
Site inspections (fabrication and construction)
Site inspections from SGS help you to ensure that your project will be completed on time and on budget, with all relevant regulations and quality standards met.
Our site inspection services include:
- Design review
- Commissioning supervision for quality and schedule
- Testing of materials, systems and installations
- Non-destructive testing supervision
- Site assessments
- Continuous supervision of construction works (quality, schedule and budget)
- Independent third party verification and certification
- Provision of quality personnel to work on your behalf
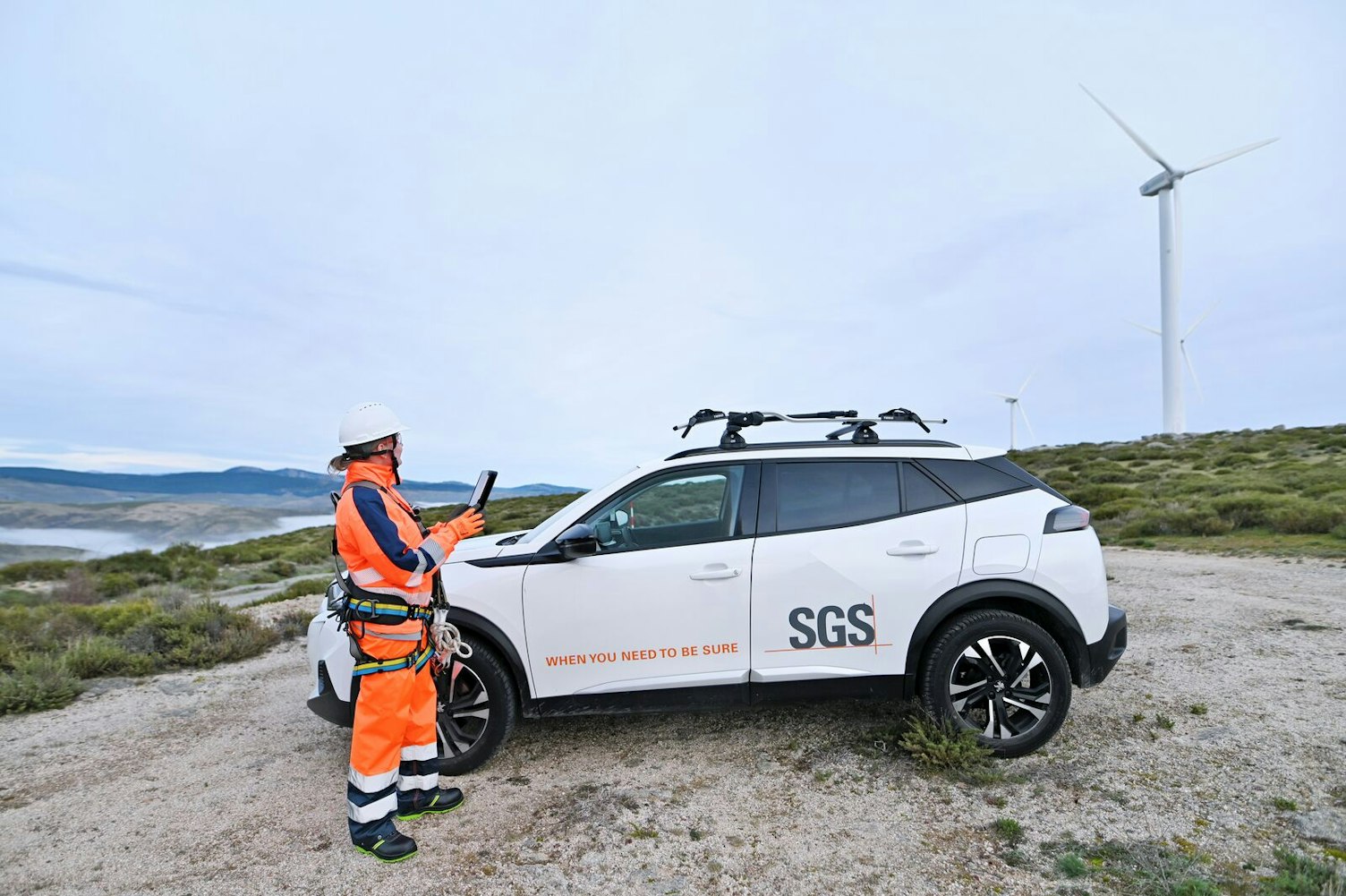
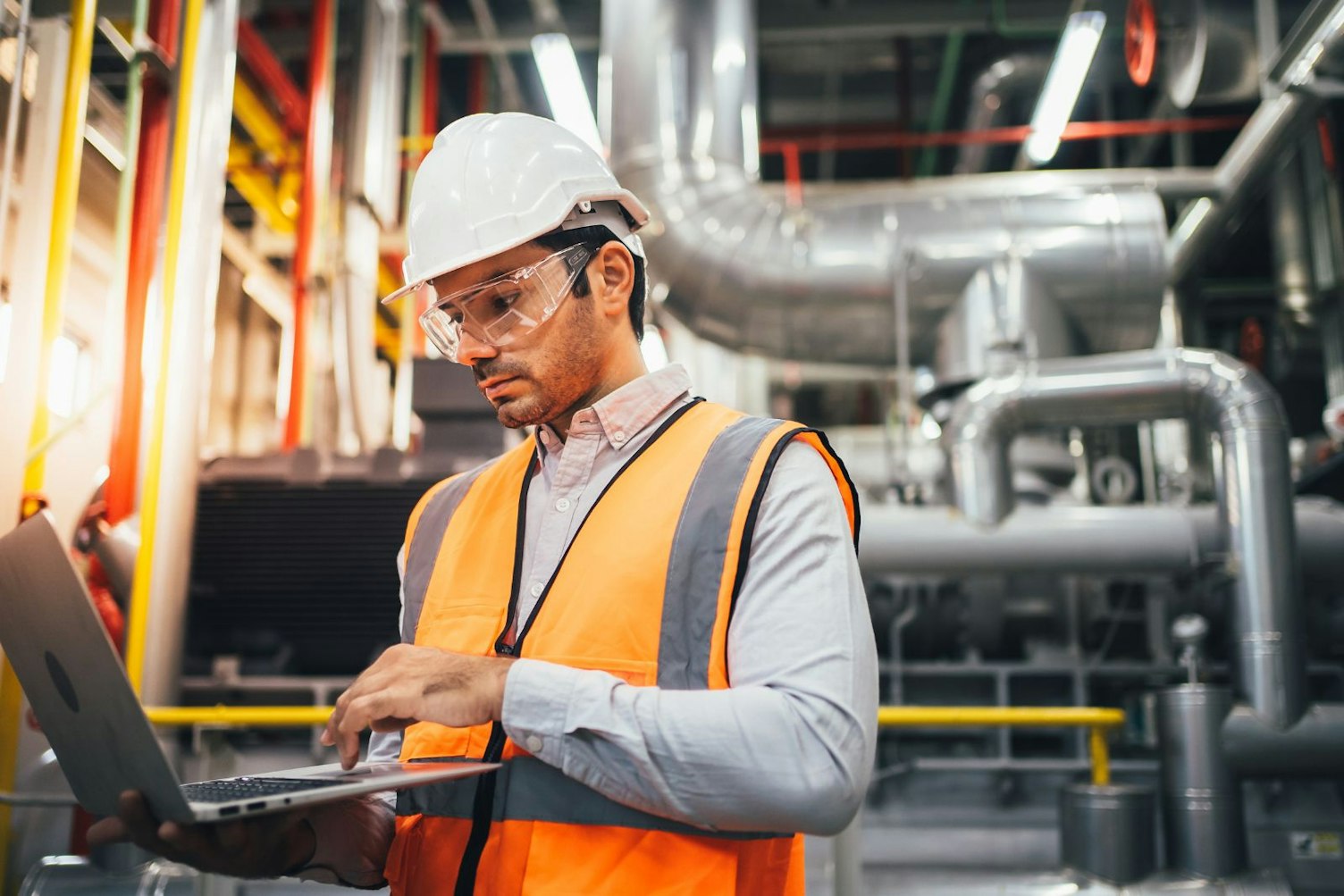
Remote inspections
Traditional inspections can be costly and time consuming and, depending on the location, qualified inspectors might not be readily available. Nevertheless, inspections are essential for ensuring quality control, which is integral to business success, no matter where your business is located.
Because of this, we have developed an innovative remote inspection app – SGS QiiQ – which will allow you to benefit from supplier inspections where in-person inspections are not practical.
Enhanced inspection coordination with KAES
Our proprietary Key Account Execution System (KAES) sets us apart by providing seamless, end-to-end management of your inspection process. Through KAES, our coordinators handle every aspect of your inspection – from initial request to final reporting – on a single, integrated digital platform accessible across all SGS offices worldwide.
This system ensures that the most qualified inspectors are assigned to your project, with real-time progress monitoring and efficient scheduling. All inspection data is securely stored and can be accessed through the Microsoft Power BI platform for advanced analytics and detailed data visualization. Developed in-house, KAES is fully customized to meet your organization’s specific needs, enhancing transparency, efficiency and the overall quality of your inspections.
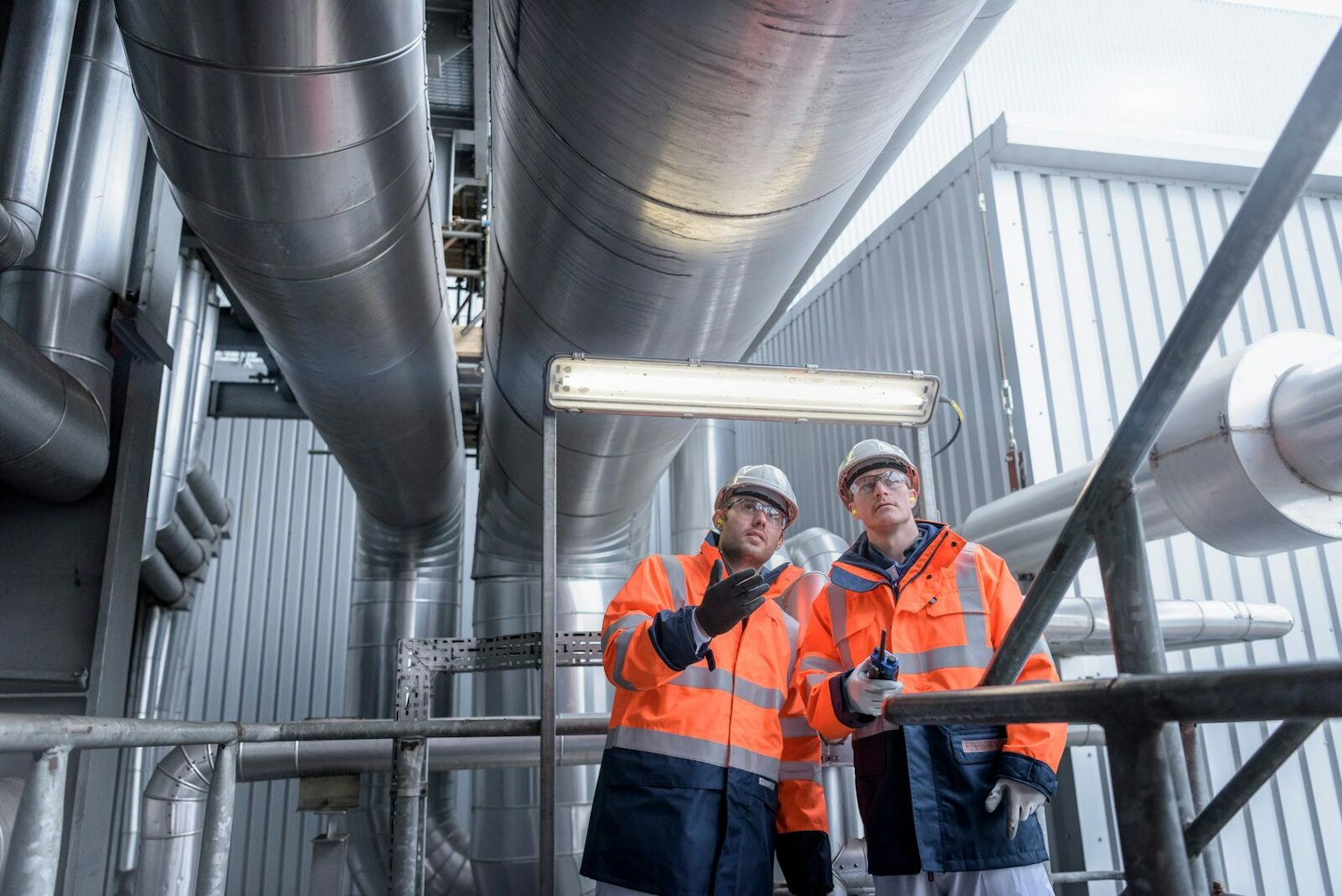
201 Route 17 North,
7th floor,
Rutherford, New Jersey, 07070,
United States